The level measurement of a container whether liquid, solid or powder in a tank, silo, hopper is achieved by the addition of load cell.
This technique makes it possible to obtain a high accuracy if you follow the rules which you find in this article.
Choosing load cells
Different technologies of load cells exist depending on the constraints of use: bending sensor, single or double shear, compression, tension.
Determination of load cells
- Compression, tension, shearing.
Number of load cells and support points.
Weighing range and load cell capacity.
Accuracy. - Operating and functional mode:
Easy assembly and maintenance.
Transmission of the signal.
Calibration - Environmental conditions:
Climate, Wind.
Temperature.
Influence of rigid bonds
Vibration - Risk control:
Seismic risk.
ATEX explosion risk.
Number of load cells and support points
Bracket and mounting kit
Each load cell is equipped with a bracket that facilitates assembly and ensures the mechanical safety of the silo and load cell. The 300 and 400 series has jack screws for the safety of the set during installation or maintenance operations. Our brackets are calculated and tested to resist parasitic forces in the 3 planes (refer to the technical sheet of bracket).
Accuracy
Weighing accuracy is the measurement error for a load, do confuse with the display rung (multiple of 1, 2, 5). Accuracy depends on several factors:
- Load cell errors < (0.01%).
- Calibration error (automatic calibration of the indicator 0.1% or with standard masses < 0.01% ).
- Mechanical error (mechanical constraint of the ducts, bridge, cone supports …) of up to 1 t in practice.
- Combined load cell Error: E-N x Load cell.
Display and signal transmission
The LOCAL display allows signal processing and conditioning as close as possible to the source. In addition, the display is very practical for maintenance and diagnosis.
– Generally it is equipped with an analog output (4-20mA) or digital (ETHERNET, PROFINET, PROFIBUS, MODBUS…).
Bending sensor
Bending or simple shearing
Weighing range 10 to 5,000 kg
Series 300
Easy implementation
Integrated security
Accuracy < (0.05%)
– Limited in maximum capacity
Double shear sensor
Weighing range 5 to 100 t
Series 400
Easy implementation: effort is distributed and centered
Integrated security
Mechanical reliability (double supports)
– Accuracy ( < 0.1% )
Compression sensor
Weighing range 15 to 500 t
Series 700
Used for heavy loads > (100 t)
Load descents on selfcentering column, simplifying the design of the supports
– Very sensitive to misalignment of support
– No built-in sensor security.
Tension sensor


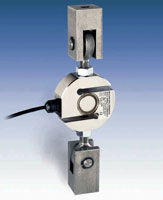
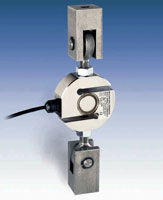
0 Comments